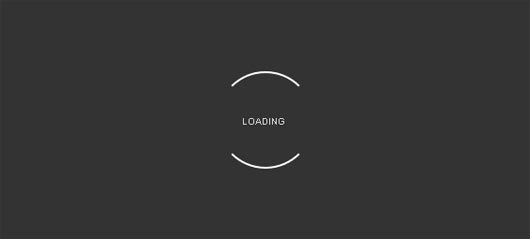
Analysis on Digital Closed-loop Manufacturing Technology of Aviation Spiral Bevel Gear
Spiral bevel gears have smooth transmission properties, are suitable for high-speed transmission, and have the advantages of very low noise and vibration, so they are often used as important gear transmission parts in aviation. This paper takes the aviation precision spiral bevel gear as the research object. First, the spiral bevel gear is theoretically modeled, then the contact imprint is analyzed by simulation, and finally the processing verification is carried out. Through feedback iterative optimization, a closed-loop manufacturing system of the spiral bevel gear is formed to solve its processing difficulties, the problem of difficult pairing.
Because the spiral bevel gear has smooth transmission, it is suitable for high-speed transmission, and the noise and vibration are very small, so it is often used as an important gear transmission part in aviation. Due to the large load and high rotational speed that need to be carried during the working process, the precision requirements of the bevel gear are often extremely strict in the design. The focus of the spiral bevel gear development lies in the tooth surface processing and detection technology of the spiral bevel gear. The tooth surface of the aviation spiral bevel gear generally needs to undergo arc milling first, then heat treatment, and finally the process route of arc grinding, and pass the gear measuring instrument inspection and meshing machine meshing inspection. . The dynamic imprint of the spiral bevel gear has a direct impact on the smooth operation, service life and noise of the gear, so it is particularly important to control the tooth surface of the spiral bevel gear.
Through the application of digital closed-loop manufacturing technology, the coordination and unity of design, manufacturing and testing can be achieved, and engineering, standardized, efficient, high-quality, and low-cost manufacturing can be achieved. The interchangeability of the spiral bevel gear and the adjustment-free assembly imprint are realized, and the application has a wide prospect and has significant economic and social benefits.
Digital Modeling Technology of Spiral Bevel Gear
Use the spiral bevel gear calculation software to conduct simulated contact imprint analysis, first compare the calculated meshing area with the actual meshing area obtained by rolling, check the simulation fit, and then compare and analyze with the contact area required by the design, so as to obtain the need for adjustment. parameters, optimize this process repeatedly, and finally get a qualified imprint.
Spiral bevel gear modeling process
Taking the spiral bevel gear pair of the main reducer as an example, the digital modeling process of the spiral bevel gear is described in detail below. Carry out basic calculations according to the relevant dimensions of the design drawing. First, input the basic data of the pair of spiral bevel gears into the software according to the part drawing, such as shaft angle, number of teeth, modulus, helix angle, rotation direction and pressure angle, etc.
After inputting the basic data of the tooth, input the parameters of the tooth shape, such as tooth height variation coefficient, tooth thickness variation coefficient, tooth tip height angle, tooth root height angle, average normal tooth thickness chord, big end full tooth height and big end tooth top
Simulation Analysis of Meshing Imprint
By continuously adjusting the modification parameters such as helix angle error, pressure angle error, drum shape in the direction of tooth length, drum shape in the direction of tooth height, and diagonal deformation in the direction of tooth length, until the static impression meets the design requirements
Spiral bevel gear machining process
The traditional spiral bevel gear processing adopts the five-knife method. First, the large wheel is processed, and then the concave and convex surfaces of the small wheel are adjusted and processed, and the static meshing imprint is checked on the meshing machine. Delivered paired with a small wheel. However, this will lead to the lack of interchangeability of large and small wheels of different batches of parts, which may lead to the risk of scrapping in pairs after repair, resulting in huge cost waste. In order to solve the above problems, it is necessary to establish an electronic standard gear, so that the tooth surface morphology before and after heat treatment is consistent, the grinding allowance is uniform after heat treatment, and the large and small wheels with inconsistent batches can also be interchanged, which not only saves costs, but also Improved part quality.
Detection and Error Compensation Technology of Spiral Bevel Gears
With the development of bevel gear processing and inspection technology, bevel gear tooth surface inspection and error compensation feedback technology has been developed from traditional contact impression inspection to accurate measurement of tooth surface profile, thus forming a closed-loop system for the entire manufacturing. The precision detection and error compensation technology of spiral bevel gear is the key link of closed-loop manufacturing technology. The closed-loop system is basically summarized as follows: use a computer to create a virtual gear model before machining bevel gears, and analyze the contact area and motion error of the tooth surface, correct the contact area and motion error of the tooth surface, and finally obtain reasonable machine tool adjustment parameters for initial machining. and tool parameter values to test the part. Import the digital theoretical model into the spiral bevel gear measuring machine, measure the processed parts, and then use the computer workstation to reverse the spiral bevel gear, give the trimming data, reprocess the parts, and then measure until the part topography meets the requirements.
According to the digital results of the spiral bevel gear, the gear processing technology and processing method are formulated, and the grinding tooth surface processing parameters are obtained through the simulation analysis of the software, and the processing parameters are optimized according to the comparison between the actual impression and the theoretical impression. According to the adjusted topography, the big wheel and the small wheel are processed respectively, and then the assembly test is carried out.
In this paper, the digital closed-loop manufacturing of spiral bevel gears is discussed by computer simulation technology. On the basis of mathematical modeling of spiral bevel gears, combined with the boundary conditions of actual working conditions, the tooth surface is accurately designed. Firstly, the static and dynamic analysis of the meshing imprint was carried out, and then the stress simulation was carried out, the topography map was established, and the three-dimensional coordinate points of the tooth surface were obtained. Use digital detection methods to feedback and compensate the processing results to form a complete digital closed-loop processing system. The processed physical products have passed the strict examination and verification, which fully proves that the method has certain engineering application value.
Because the spiral bevel gear has smooth transmission, it is suitable for high-speed transmission, and the noise and vibration are very small, so it is often used as an important gear transmission part in aviation. Due to the large load and high rotational speed that need to be carried during the working process, the precision requirements of the bevel gear are often extremely strict in the design. The focus of the spiral bevel gear development lies in the tooth surface processing and detection technology of the spiral bevel gear. The tooth surface of the aviation spiral bevel gear generally needs to undergo arc milling first, then heat treatment, and finally the process route of arc grinding, and pass the gear measuring instrument inspection and meshing machine meshing inspection. . The dynamic imprint of the spiral bevel gear has a direct impact on the smooth operation, service life and noise of the gear, so it is particularly important to control the tooth surface of the spiral bevel gear.
Through the application of digital closed-loop manufacturing technology, the coordination and unity of design, manufacturing and testing can be achieved, and engineering, standardized, efficient, high-quality, and low-cost manufacturing can be achieved. The interchangeability of the spiral bevel gear and the adjustment-free assembly imprint are realized, and the application has a wide prospect and has significant economic and social benefits.
Digital Modeling Technology of Spiral Bevel Gear
Use the spiral bevel gear calculation software to conduct simulated contact imprint analysis, first compare the calculated meshing area with the actual meshing area obtained by rolling, check the simulation fit, and then compare and analyze with the contact area required by the design, so as to obtain the need for adjustment. parameters, optimize this process repeatedly, and finally get a qualified imprint.
Spiral bevel gear modeling process
Taking the spiral bevel gear pair of the main reducer as an example, the digital modeling process of the spiral bevel gear is described in detail below. Carry out basic calculations according to the relevant dimensions of the design drawing. First, input the basic data of the pair of spiral bevel gears into the software according to the part drawing, such as shaft angle, number of teeth, modulus, helix angle, rotation direction and pressure angle, etc.
After inputting the basic data of the tooth, input the parameters of the tooth shape, such as tooth height variation coefficient, tooth thickness variation coefficient, tooth tip height angle, tooth root height angle, average normal tooth thickness chord, big end full tooth height and big end tooth top
Simulation Analysis of Meshing Imprint
By continuously adjusting the modification parameters such as helix angle error, pressure angle error, drum shape in the direction of tooth length, drum shape in the direction of tooth height, and diagonal deformation in the direction of tooth length, until the static impression meets the design requirements
Spiral bevel gear machining process
The traditional spiral bevel gear processing adopts the five-knife method. First, the large wheel is processed, and then the concave and convex surfaces of the small wheel are adjusted and processed, and the static meshing imprint is checked on the meshing machine. Delivered paired with a small wheel. However, this will lead to the lack of interchangeability of large and small wheels of different batches of parts, which may lead to the risk of scrapping in pairs after repair, resulting in huge cost waste. In order to solve the above problems, it is necessary to establish an electronic standard gear, so that the tooth surface morphology before and after heat treatment is consistent, the grinding allowance is uniform after heat treatment, and the large and small wheels with inconsistent batches can also be interchanged, which not only saves costs, but also Improved part quality.
Detection and Error Compensation Technology of Spiral Bevel Gears
With the development of bevel gear processing and inspection technology, bevel gear tooth surface inspection and error compensation feedback technology has been developed from traditional contact impression inspection to accurate measurement of tooth surface profile, thus forming a closed-loop system for the entire manufacturing. The precision detection and error compensation technology of spiral bevel gear is the key link of closed-loop manufacturing technology. The closed-loop system is basically summarized as follows: use a computer to create a virtual gear model before machining bevel gears, and analyze the contact area and motion error of the tooth surface, correct the contact area and motion error of the tooth surface, and finally obtain reasonable machine tool adjustment parameters for initial machining. and tool parameter values to test the part. Import the digital theoretical model into the spiral bevel gear measuring machine, measure the processed parts, and then use the computer workstation to reverse the spiral bevel gear, give the trimming data, reprocess the parts, and then measure until the part topography meets the requirements.
According to the digital results of the spiral bevel gear, the gear processing technology and processing method are formulated, and the grinding tooth surface processing parameters are obtained through the simulation analysis of the software, and the processing parameters are optimized according to the comparison between the actual impression and the theoretical impression. According to the adjusted topography, the big wheel and the small wheel are processed respectively, and then the assembly test is carried out.
In this paper, the digital closed-loop manufacturing of spiral bevel gears is discussed by computer simulation technology. On the basis of mathematical modeling of spiral bevel gears, combined with the boundary conditions of actual working conditions, the tooth surface is accurately designed. Firstly, the static and dynamic analysis of the meshing imprint was carried out, and then the stress simulation was carried out, the topography map was established, and the three-dimensional coordinate points of the tooth surface were obtained. Use digital detection methods to feedback and compensate the processing results to form a complete digital closed-loop processing system. The processed physical products have passed the strict examination and verification, which fully proves that the method has certain engineering application value.
Leave a comment