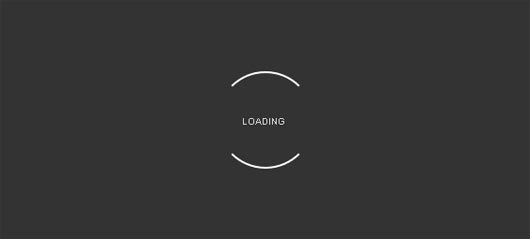
Optimization of Gear Shaping Machining Process for Long Shaft Gear Parts
At present, the processing of gears is still mainly gear hobbing and gear shaping. Different processing technologies have different characteristics. In actual processing, the most suitable processing technology is often selected according to the characteristics of the parts; the selection of different processing technologies will affect and even decide the quality and level of machining. At the current stage of gear processing technology in my country, there are still many problems that need to be considered by process designers, and new methods are constantly proposed to optimize to improve the level of gear processing technology.
The gear machining of gear parts generally adopts the gear hobbing process with high efficiency; compared with the gear hobbing process, although the gear shaping process is less efficient, its precision is better than that of the gear hobbing. In addition, the gear shaping can process internal teeth and off-axis. gears closer to the shoulder. For example, for some long shaft gear parts, due to the limitation of the shaft shoulder structure, there is not enough gear hobbing, so the gear shaping process can only be adopted. However, due to the low gear shaping efficiency, process optimization is particularly important. By designing automatic tightening fixtures and optimizing cutting parameters and allowances, the processing efficiency of gear shaping can be improved.
Figure 1 shows the power output drive shaft of the tractor parts, in which the A tooth module is 5mm and the number of teeth is 11, and the B tooth module is 5mm and the number of teeth is 13. The B teeth can be directly hobbed, while the B teeth interfere with the hob when the A teeth are directly hobbed, and can only be processed by gear shaping for a long time. The machining of shaft parts generally uses the center holes at both ends as the positioning reference, but this part is long (478mm), and the outer circle of the rod is relatively thin (Φ30mm), so the tooth shaping process of A tooth adopts the outer circle D and end face E positioning, manual Use a dial indicator to find the outer circle C of the A tooth part and process it; C, D outer circle and E end face have a fine grinding process before the tooth shaping. Moreover, the fixture needs to manually tighten four pressure plates to compress the parts. The processing efficiency and clamping efficiency are extremely low, and the labor intensity is also high. Only 15 pieces are processed per shift, which has become the processing bottleneck of this part, which seriously affects the production capacity. Figure 2 shows the manual clamping fixture before process optimization. Through the analysis of the part structure and the original process plan, it is believed that the main problem of this part processing is low processing efficiency. To solve this problem, breakthroughs can be found in the following two aspects: First, in terms of processing technology: find efficient processing methods to make up for The disadvantage of the low efficiency of the gear shaping process; second, the fixture: a new gear shaping fixture with automatic tightening and no gap positioning is designed, without manual single-piece alignment and upper platen screws, which greatly improves the clamping.
Gear hobbing is the most efficient machining process at present, but direct hobbing will have tool interference. So I thought of the combination of gear hobbing and gear shaping, that is, gear hobbing only removes most of the machining allowance without processing it to size, and the remaining allowance is processed by gear shaping to size, which can avoid tool interference, It can also achieve the purpose of improving efficiency. To design automatic tightening, the first thing to consider is the part structure. Due to the relatively long structure of the parts, it is more difficult to design fixtures: the length of the parts is 478mm, and most of the lengths must be installed on the work surface of the machine tool, which basically reaches the processing limit of the machine tool. According to the conventional design, the fixture is extremely difficult to manufacture, the manufacturing accuracy is difficult to guarantee, the weight is also very large, and the price will be very expensive.
Through the theoretical analysis and drawing of the part (see Figure 1), it is found that the interference of hobbing at A is small. For example, reducing the common normal of hobbing by 1mm can just complete the hobbing; after rough hobbing, use The gear shaping process processes the remaining allowance of the teeth to complete the final tooth shape processing. In this way, the process is divided into two parts, the machining allowance of the two processing methods is small, and large feed processing can be used, and the efficiency of the hobbing process is inherently high, so the processing efficiency will be doubled.
After analyzing the original process, the outer circle D and the end face E are the ground datums, so the new fixture is still positioned on the outer circle D and the end face E. The schematic diagram of its assembly is shown in Figure 2. The previous low machining accuracy was mainly caused by the gap positioning between the outer circle D and the fixture, and the manual alignment accuracy was not high; the new fixture uses an elastic collet to hold the outer circle D, and there is no gap for positioning, and there is no need to align the outer circle of the tooth; the elastic cylinder The clamp is connected with the hydraulic cylinder of the machine tool through the connecting nut, the connecting rod and the tie rod, and the automatic positioning and tightening process of the parts is completed with the action of the hydraulic cylinder of the machine tool. Four long tie rods are used to connect the elastic collet and the hydraulic cylinder of the machine tool, which not only avoids the long part rod, but also does not cause the clamp to be overweight, saves materials and reduces the cost of the clamp. The upper body is equipped with a manual tooth alignment gauge. After the first piece is adjusted, the subsequent tooth alignment gauge can ensure the correspondence between the tooth grooves of each part and the cutter teeth. Since the common normal line has a margin of 1mm, the tooth alignment is convenient and fast, and it can also meet the Requirements for gear shaping accuracy.
Before the implementation of the new process, due to the low efficiency of gear shaping and clamping, only 15 pieces were processed per shift. After the new process was adopted, the rough rolling process was 60 pieces per shift, and the fine plugging process was 35 pieces per shift, which doubled the processing time. In addition, the precision of the parts is also greatly improved, and the gear-shaping clamping does not need to be aligned, so the hot pre-finishing process of the outer circle C of the tooth portion is cancelled. This part uses the rough hobbing process, which must be checked and processed through experiments, and the size of the common normal line and the knife cutting are strictly controlled to avoid interference with the B tooth caused by excessive cutting; processing. In addition, the gear shaping process should mainly pay attention to the operation of the teeth, so as to avoid the inaccuracy of the teeth and the tooth surface cannot be fully processed.
Through the innovative optimization of the process plan and the innovative design of the gear shaping fixture, while improving the processing efficiency, the processing quality of the parts is improved, the redundant grinding process is reduced, the overall optimization of the process is achieved, and the processing of special parts in the future. A new process scheme is provided. Therefore, the mechanical process design and optimization can only find a solution by breaking through the traditional processing thinking, and based on the theory and carry out continuous practical verification, can it become a feasible and innovative solution.
Article Source: 齿轮传动
The gear machining of gear parts generally adopts the gear hobbing process with high efficiency; compared with the gear hobbing process, although the gear shaping process is less efficient, its precision is better than that of the gear hobbing. In addition, the gear shaping can process internal teeth and off-axis. gears closer to the shoulder. For example, for some long shaft gear parts, due to the limitation of the shaft shoulder structure, there is not enough gear hobbing, so the gear shaping process can only be adopted. However, due to the low gear shaping efficiency, process optimization is particularly important. By designing automatic tightening fixtures and optimizing cutting parameters and allowances, the processing efficiency of gear shaping can be improved.
1. Workpiece Structure and Current Situation Analysis
Figure 1 shows the power output drive shaft of the tractor parts, in which the A tooth module is 5mm and the number of teeth is 11, and the B tooth module is 5mm and the number of teeth is 13. The B teeth can be directly hobbed, while the B teeth interfere with the hob when the A teeth are directly hobbed, and can only be processed by gear shaping for a long time. The machining of shaft parts generally uses the center holes at both ends as the positioning reference, but this part is long (478mm), and the outer circle of the rod is relatively thin (Φ30mm), so the tooth shaping process of A tooth adopts the outer circle D and end face E positioning, manual Use a dial indicator to find the outer circle C of the A tooth part and process it; C, D outer circle and E end face have a fine grinding process before the tooth shaping. Moreover, the fixture needs to manually tighten four pressure plates to compress the parts. The processing efficiency and clamping efficiency are extremely low, and the labor intensity is also high. Only 15 pieces are processed per shift, which has become the processing bottleneck of this part, which seriously affects the production capacity. Figure 2 shows the manual clamping fixture before process optimization. Through the analysis of the part structure and the original process plan, it is believed that the main problem of this part processing is low processing efficiency. To solve this problem, breakthroughs can be found in the following two aspects: First, in terms of processing technology: find efficient processing methods to make up for The disadvantage of the low efficiency of the gear shaping process; second, the fixture: a new gear shaping fixture with automatic tightening and no gap positioning is designed, without manual single-piece alignment and upper platen screws, which greatly improves the clamping.

2. efficiency and the gear shaping accuracy
Gear hobbing is the most efficient machining process at present, but direct hobbing will have tool interference. So I thought of the combination of gear hobbing and gear shaping, that is, gear hobbing only removes most of the machining allowance without processing it to size, and the remaining allowance is processed by gear shaping to size, which can avoid tool interference, It can also achieve the purpose of improving efficiency. To design automatic tightening, the first thing to consider is the part structure. Due to the relatively long structure of the parts, it is more difficult to design fixtures: the length of the parts is 478mm, and most of the lengths must be installed on the work surface of the machine tool, which basically reaches the processing limit of the machine tool. According to the conventional design, the fixture is extremely difficult to manufacture, the manufacturing accuracy is difficult to guarantee, the weight is also very large, and the price will be very expensive.
3. Processing plan optimization
Through the theoretical analysis and drawing of the part (see Figure 1), it is found that the interference of hobbing at A is small. For example, reducing the common normal of hobbing by 1mm can just complete the hobbing; after rough hobbing, use The gear shaping process processes the remaining allowance of the teeth to complete the final tooth shape processing. In this way, the process is divided into two parts, the machining allowance of the two processing methods is small, and large feed processing can be used, and the efficiency of the hobbing process is inherently high, so the processing efficiency will be doubled.
4. Automatic Fixture Design
After analyzing the original process, the outer circle D and the end face E are the ground datums, so the new fixture is still positioned on the outer circle D and the end face E. The schematic diagram of its assembly is shown in Figure 2. The previous low machining accuracy was mainly caused by the gap positioning between the outer circle D and the fixture, and the manual alignment accuracy was not high; the new fixture uses an elastic collet to hold the outer circle D, and there is no gap for positioning, and there is no need to align the outer circle of the tooth; the elastic cylinder The clamp is connected with the hydraulic cylinder of the machine tool through the connecting nut, the connecting rod and the tie rod, and the automatic positioning and tightening process of the parts is completed with the action of the hydraulic cylinder of the machine tool. Four long tie rods are used to connect the elastic collet and the hydraulic cylinder of the machine tool, which not only avoids the long part rod, but also does not cause the clamp to be overweight, saves materials and reduces the cost of the clamp. The upper body is equipped with a manual tooth alignment gauge. After the first piece is adjusted, the subsequent tooth alignment gauge can ensure the correspondence between the tooth grooves of each part and the cutter teeth. Since the common normal line has a margin of 1mm, the tooth alignment is convenient and fast, and it can also meet the Requirements for gear shaping accuracy.

5. The effect of the new process plan
Before the implementation of the new process, due to the low efficiency of gear shaping and clamping, only 15 pieces were processed per shift. After the new process was adopted, the rough rolling process was 60 pieces per shift, and the fine plugging process was 35 pieces per shift, which doubled the processing time. In addition, the precision of the parts is also greatly improved, and the gear-shaping clamping does not need to be aligned, so the hot pre-finishing process of the outer circle C of the tooth portion is cancelled. This part uses the rough hobbing process, which must be checked and processed through experiments, and the size of the common normal line and the knife cutting are strictly controlled to avoid interference with the B tooth caused by excessive cutting; processing. In addition, the gear shaping process should mainly pay attention to the operation of the teeth, so as to avoid the inaccuracy of the teeth and the tooth surface cannot be fully processed.
Through the innovative optimization of the process plan and the innovative design of the gear shaping fixture, while improving the processing efficiency, the processing quality of the parts is improved, the redundant grinding process is reduced, the overall optimization of the process is achieved, and the processing of special parts in the future. A new process scheme is provided. Therefore, the mechanical process design and optimization can only find a solution by breaking through the traditional processing thinking, and based on the theory and carry out continuous practical verification, can it become a feasible and innovative solution.
Article Source: 齿轮传动
Leave a comment